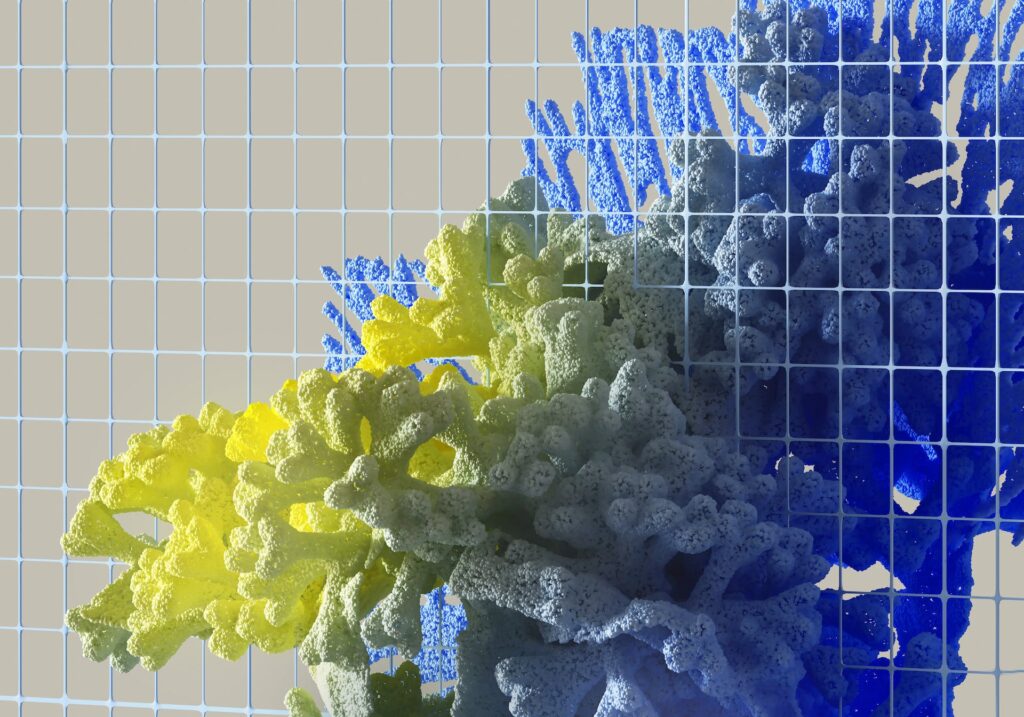
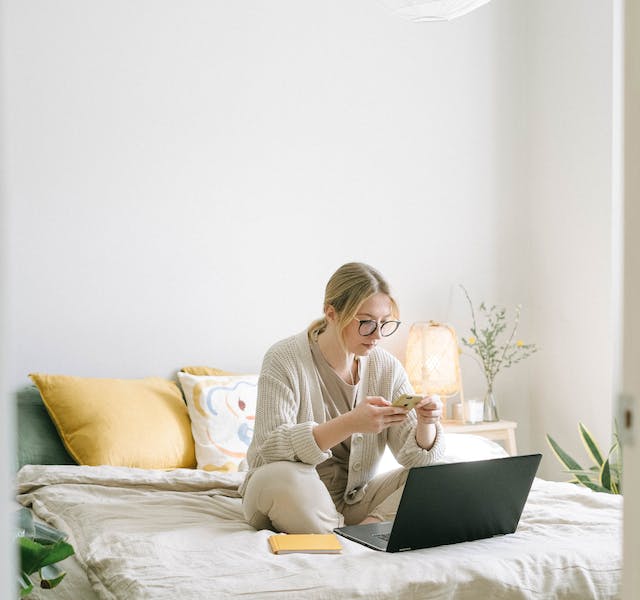
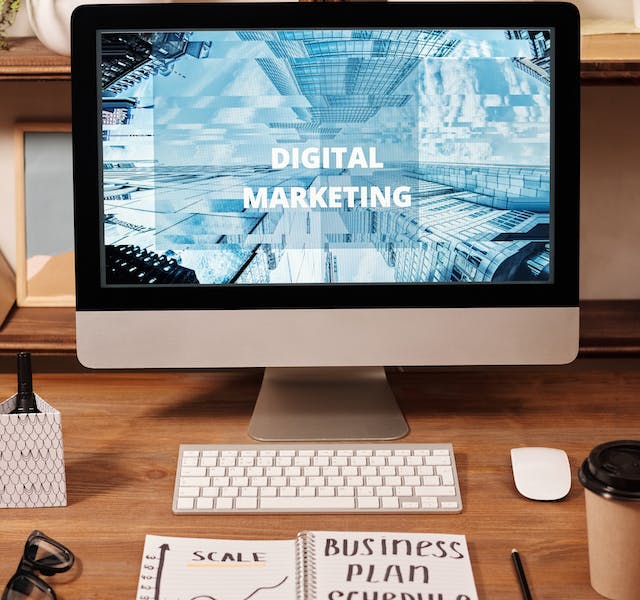
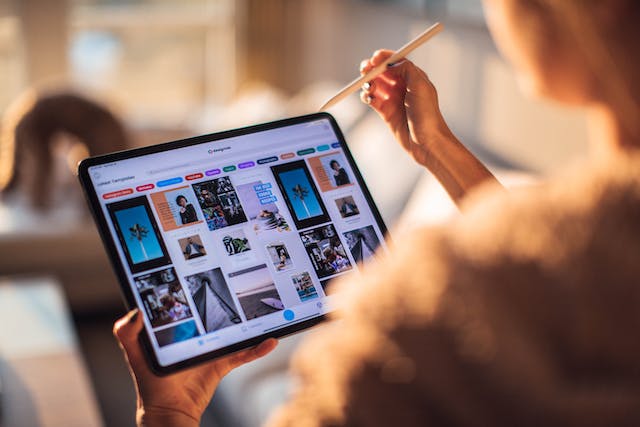
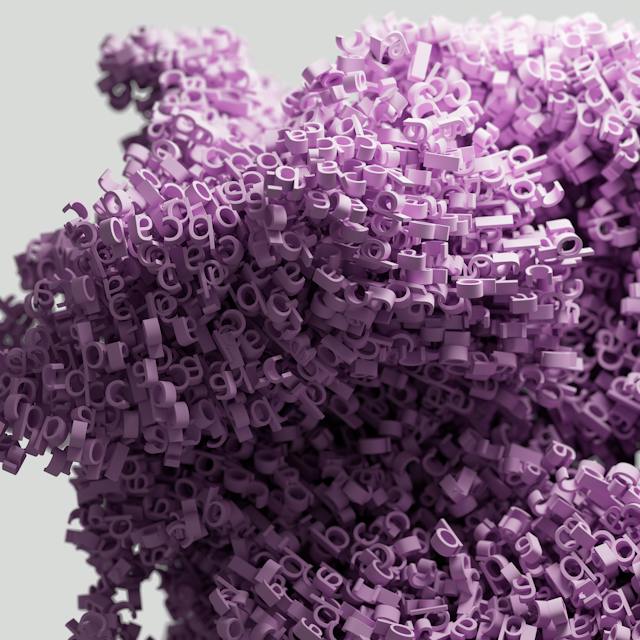
About Us
Digital Twin Technology stands at the forefront of digital innovation, specializing in the development and application of digital twin solutions. This professional platform offers in-depth insights into how digital twins—virtual models of physical entities, powered by real-time data—drive efficiency and strategic decision-making across various sectors. Catering to industry professionals and tech enthusiasts, the site serves as a hub for exploring the transformative impacts and practical implementations of digital twin technology in the modern digital landscape.
Our Services
At Digital Twin Technology, we specialize in the advanced field of digital twin development and implementation. Our services focus on creating dynamic virtual replicas of physical entities, utilizing real-time data for comprehensive analysis and simulation. These offerings are essential for businesses aiming to enhance operational efficiency, predictive maintenance, and strategic planning. Our expertise caters to a wide range of industries, making us a go-to resource for professionals seeking to integrate cutting-edge digital twin technologies in their operations.
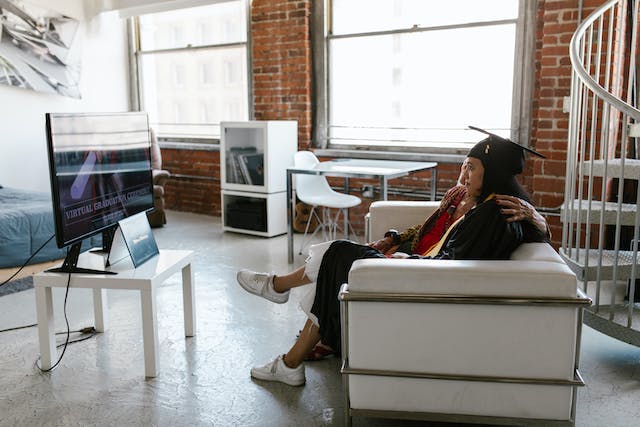
Dynamic Virtual Modeling
Creating real-time virtual replicas of physical systems.
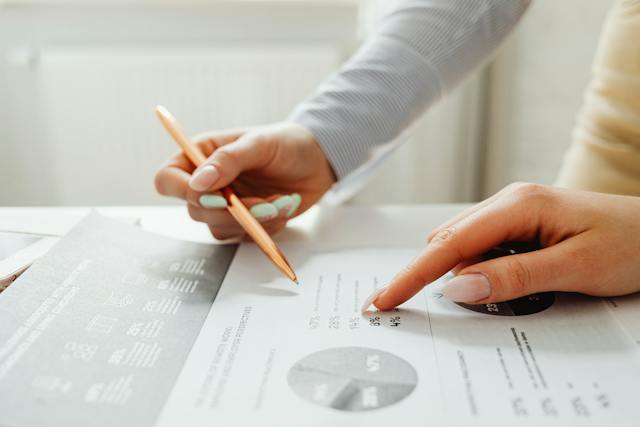
Data Analysis and Simulation
Utilizing real-time data for in-depth analysis and predictive simulations.
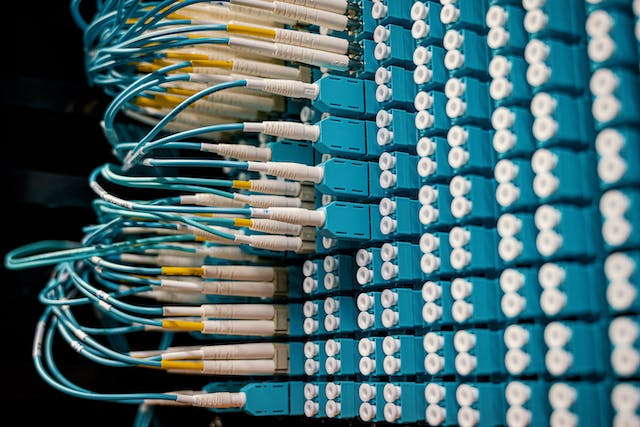
Operational Efficiency Enhancement
Tools and strategies to improve business processes and resource management.
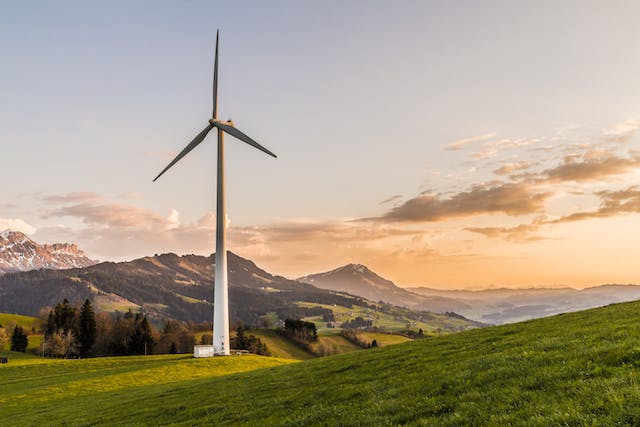
Predictive Maintenance Solutions
Advanced forecasting to preemptively address maintenance needs.
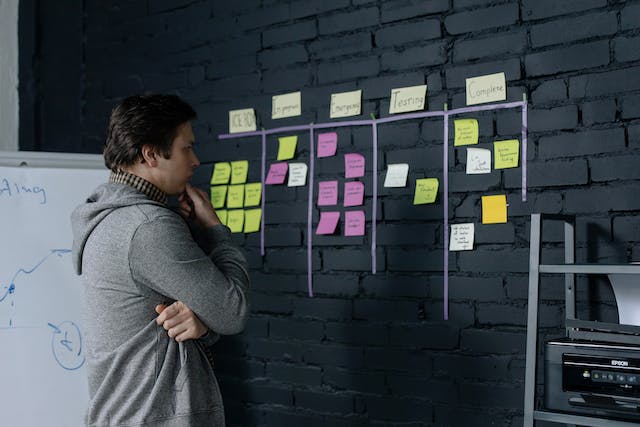
Strategic Planning Assistance
Leveraging digital twins for informed decision-making and future planning.
Why Choose Us
- Expertise and Experience
Our team is highly skilled and brings years of experience in our field, ensuring that you receive knowledgeable and professional service.
-
Customer-Centric Approach
We prioritize our customers’ needs and preferences, offering personalized services and support to ensure satisfaction.
Innovative Solutions
We stay at the forefront of our industry, incorporating the latest technologies and innovative strategies to provide the best possible service or product.
-
Quality Assurance
We are committed to high standards of quality, and our products/services undergo rigorous testing to ensure reliability and excellence.
Competitive Pricing
We offer competitive pricing without compromising on quality, ensuring you receive great value for your investment.
Discover How Our Digital Twin Technology Can Transform Your Business Today!
Embrace Digital Twin Technology with us and see immediate transformation in your business. Our expert team will tailor a solution that aligns seamlessly with your operations, offering real-time insights and analytics to optimize performance and reduce costs. We ensure a smooth integration and continuous support, helping you stay ahead in innovation and efficiency. Partner with us for a future where technology not only predicts but powers your success.
Contact Digital Twin Technology
123 Tech Street, Innovation Park
San Diego, CA 92101, USA
contact@digitaltwintechnology.net
+1 619-555-0123